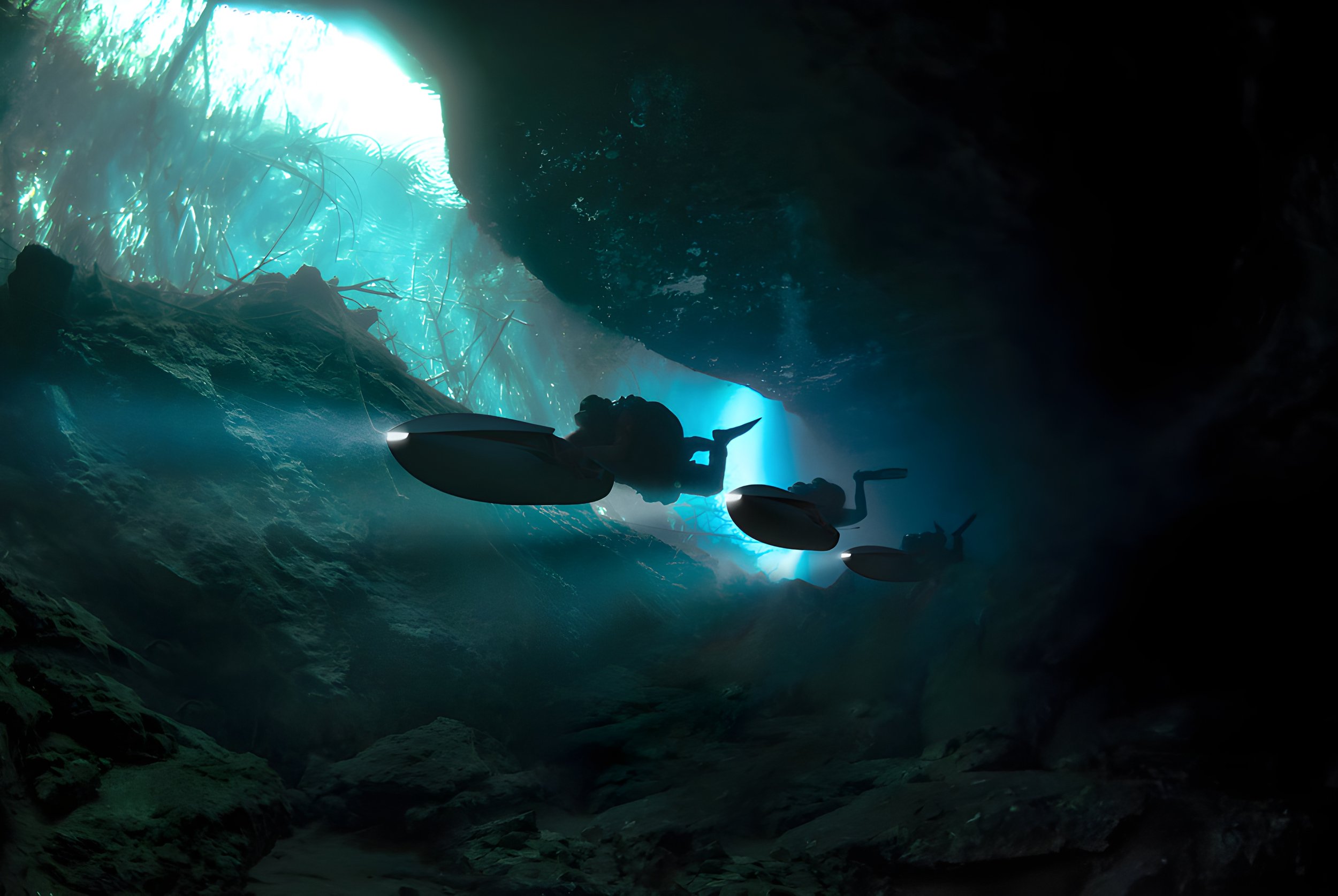
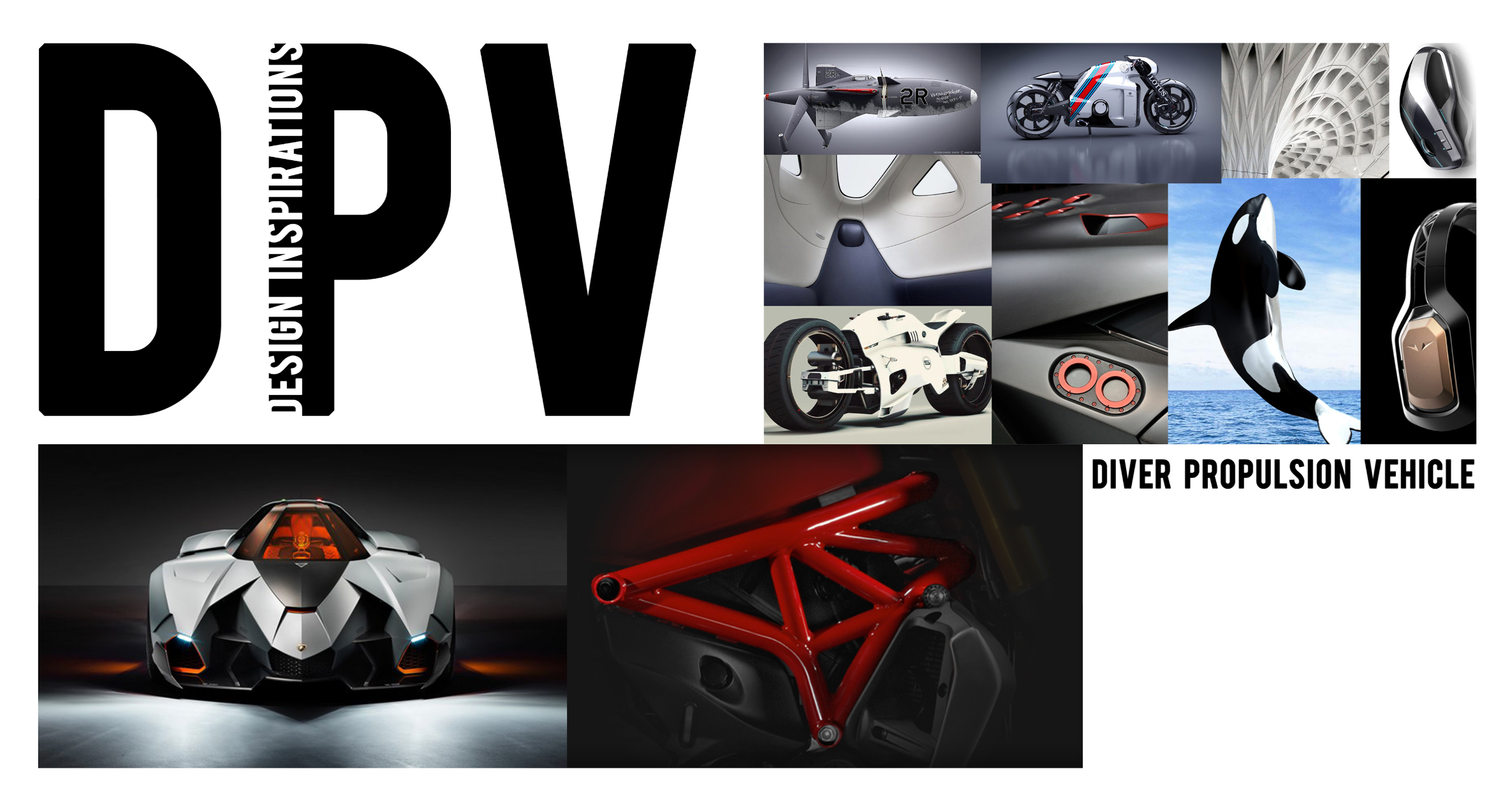
The Dive Propulsion Vehicle is a game-changer for military underwater operations, offering speed and agility. Built for performance and durability, it features a lightweight design, making it easy to transport and use in challenging conditions. With advanced technology and expert craftsmanship, the DPV enhances tactical missions, providing reliable and efficient underwater mobility for military divers and special forces.
The process of ideation in sketches for a military Dive Propulsion Vehicle (DPV) begins with brainstorming to generate ideas, followed by creating quick, rough sketches to capture various concepts. These initial sketches are then reviewed, and the most promising ones are selected for further detailing and refinement, focusing on functionality and form. Technical details and dimensions are incorporated to ensure usability, considering materials and construction methods. Polished presentation sketches are created, showcasing the DPV in context with annotations explaining key features. Finally, the best design is chosen based on feedback and feasibility, with detailed, high-quality sketches produced for documentation and further development, capturing the entire ideation process and the final concept.
When the development begins
The process of Computer-Aided Design (CAD) involves several steps to create precise digital models. It begins with conceptualization, where designers outline their ideas and requirements. This is followed by creating a preliminary sketch or 2D drawing using CAD software. Designers then develop these drawings into detailed 3D models, refining the design by adding dimensions, features, and materials. The next step involves running simulations and analyses to test the design’s functionality and performance under various conditions. Based on the results, adjustments are made to improve the design. Once finalized, the CAD model is used to generate detailed technical drawings and specifications for manufacturing. This process ensures accuracy, efficiency, and the ability to easily modify designs as needed.
Creating a scale model involves several key steps to accurately represent a design at a reduced size. First, the original design or object is carefully measured and analyzed to determine the appropriate scale, ensuring that all proportions are maintained. Detailed sketches or CAD drawings are then created to guide the modeling process. Next, materials suitable for the scale model are selected, often including plastic, wood, or metal, depending on the required detail and durability. The model is then constructed, meticulously following the scaled-down dimensions. Throughout the construction process, precise measurements and adjustments are made to ensure accuracy. Finally, the scale model is finished with appropriate detailing, such as paint, textures, and any movable parts, to closely resemble the original design.
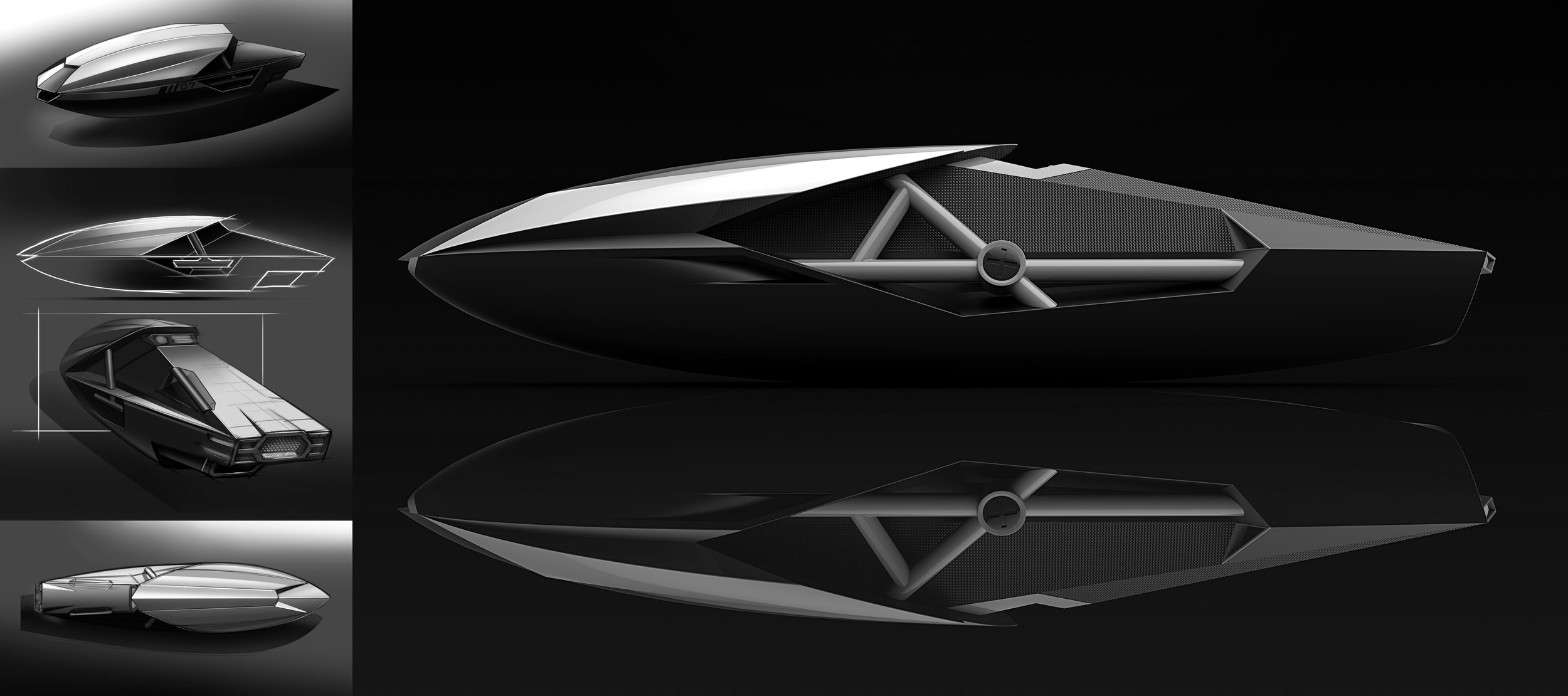